Following a set of standards is crucial for businesses to ensure their products and services can meet a level of quality that promotes customer satisfaction. At Progressive Automations, we aim for nothing but the best for our customers and strive toward continual improvements. Because of this, we are excited to announce that Progressive Automations is now ISO 9001:2015 certified! This article will cover why our recent ISO 9001:2015 certification is important for improving our Quality Management Systems to bring the best possible quality and services to our customers.
What the ISO 9001:2015 Certification Means

The International Organization for Standardization (ISO) is an organization responsible for international standard development. The requirement for an organization to follow a Quality Management System (QMS) is known as ISO 9001:2015. Requirements in a Quality Management System include:
- Consistency to meet customers’ needs through quality products and services
- Continual improvements in procedures and processes to enhance customer satisfaction
- Ensuring conformity with all relevant regulatory and statutory requirements
To become ISO 9001:2015 certified, an accredited registrar for ISO 9001 QMS performs audits of a company’s Quality Management Systems to ensure full compliance and commitment to customer satisfaction.
How This Certification Affects the Delivery of Our Products

The adoption of our new Quality Management System builds up the process changes we have made to ensure we meet or exceed minimum standards. Starting from the very first point of contact with our customers and to after-sales service, our linear actuators, home & office solutions, and motion control products go through our rigorous processes to ensure customer satisfaction:
- Customer Communication
- Review Process
- Sampling Process
- Non-Conformance Report (NCR)
- Purchase Orders
- Mass Production
- Quality Control (QC)
- After-Sales Service
Customer Communication
The moment we communicate with our customers, we make sure to capture their product requirements. By logging customer product requirements into our records, we have the means to go back and check them if needed to ensure there will be no issues with compatibility or miscommunication.
Review Process
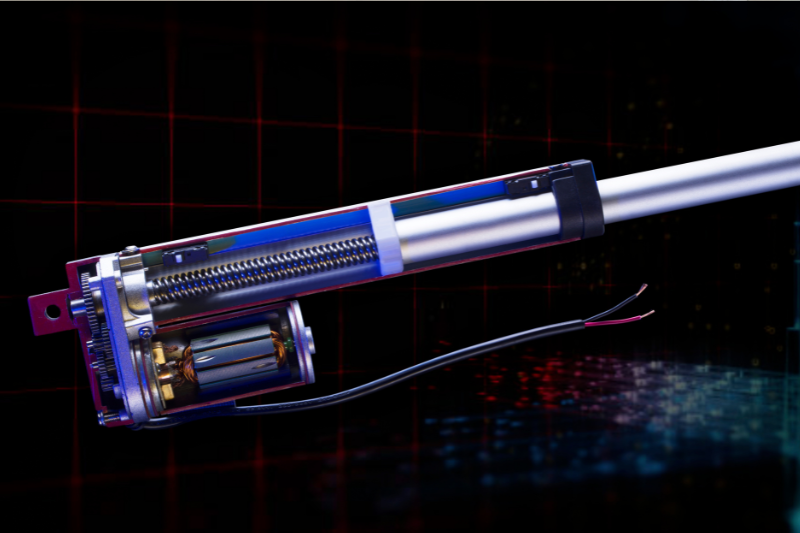
Before we commit to a solution, we double-check if the requested product requirements were feasible and something we can meet. This review process gets logged and tracked by our sales team so that both parties will have a history that they can refer to. If anything were to go wrong, we can track the history and determine where it went wrong.
Sampling Process

We collaborate with our customers on a manufacturing document to ensure our final products are solutions that will be able to meet or exceed the required quality standards. Crucial details such as the required materials, customizations, dimensions, and specifications are in the manufacturing documents.
Non-Conformance Report (NCR)
If any sample units failed to meet the minimum quality requirements, we would file a non-conformance report. We would then develop corrective procedures for these issues and investigate the problem through root cause analysis. This is to find out why the issues were happening and to then put an immediate fix in place, ensuring these issues do not happen again. The effectiveness of our procedures is tracked, verified, and reviewed by management through quarterly meetings.
Purchase Orders
Once we have established a solution that can meet all our customer’s requirements, we can then proceed with purchase orders. As customers place their purchase orders, we make sure to send purchase order confirmations to verify that the specifications and prices are correct. All purchase orders get logged in our database for records.
Mass Production

During production, manufacturing specifications are all aligned so that our facilities know exactly how the units need to be made. We make sure mass production carefully follows the manufacturing documents for the required materials, customizations, dimensions, specifications, etc.
Quality Control (QC)

Production units go through rigorous quality control inspections to ensure our products have met or exceeded the quality requirements. We perform corrective actions when there is any requirement that was not being followed. Examples can include correcting for the build tolerance, motor speed, wire insulation requirements, etc. By continuously reviewing the quality missed opportunities, our commitment to continual improvements ensures high-quality products.
After-Sales Service

After the sale of our products, we stand behind our warranty and policies throughout the whole product’s life cycle. If units were to fail in the field, we would take the units back to perform a root cause analysis and ensure accountability goes through the whole supply chain by filing supplier corrective actions.
Why This Certification Will Benefit Our Customers

Customers will benefit from knowing our quality has been audited by Perry Johnson Registrars (PJR) who is an accredited registrar for ISO 9001 QMS. These audits ensure our processes have been thoroughly inspected and that everyone in our team has been professionally trained for their roles. We have a matrix that tracks if anyone in our team needs specific training based on their job role. After employee training is completed, this gets logged into our training records which regularly verify the training effectiveness.
Regular facility inspections ensure our customers that we are following safety guidelines, fire safety inspection checklists, segregating customer property, and having non-conforming products (NCP) areas. To ensure the consistent quality of our products, we also have an approved vendor list where all vendors have to go through our checks, balances, and processes. Our entire process follows internationally accredited standards, giving customers peace of mind and trust that we follow the same process as them when it comes to manufacturing quality.
IN SUMMARY
Our recent ISO 9001:2015 certification is a result of Progressive Automations’ commitment to continual improvements in our procedures, services, products, and Quality Management System. Every day, we challenge ourselves to do our best, guarantee customer satisfaction, improve our operations, and bring innovation to our products.
As one of the top suppliers of electric linear actuators, Progressive Automations offers industry-leading flexibility, quality, support, and field experience to meet all your needs. If you have any other questions about what we can offer, please do not hesitate in reaching out to us! We are experts in what we do and want to ensure you find the best solutions for your application.
sales@progressiveautomations.com | 1-800-676-6123