In today's how to post we will be going over the steps necessary to combine linear actuator control systems together. Now in order to combine control systems, you must prevent short-circuiting as this can damage your components. Since the control boxes connect actuators to the ground when not activated we cannot use them for direct control in parallel.
When combining the systems we use diodes to allow only the current to flow away from the control box. Then the outputs are connected to relays, which isolates the system from reversing polarities of the actuator control. To help with this explanation we have provided step by step photos of the process with a brief description for each. Now let's get started. For this example, we will be combining our PA-31 and PA-35 control systems.
1. This is the process to solder a butt-splice with diodes into the leads from our control boxes. The wires are bent to give more strength when hooking them together. We also recommend using a heat shrink to protect from the elements and unwanted connections.

2. For soldering, we recommend using Soldering Paste or "Flux" as it helps the solder spread evenly with less heat.

3. Now that we've finished prepping we'll start with heating up the soldering iron. Then clean the tip of the iron using either a tip cleaner (what we are using), a damp towel or a sponge.

4. Apply some solder directly to the tip of the wire. This makes it easier for heat to transfer to the wire.

5. Apply some heat to the wire and add more solder. This will secure the connection but be careful, too much heat can damage the diode.

6. Tin the end of the wires to prevent fraying. (Side Note: Warning, soldering produces toxic fumes, make sure you are in a well-ventilated area or use a fume extractor before soldering, and do not forget to turn it off when finished).
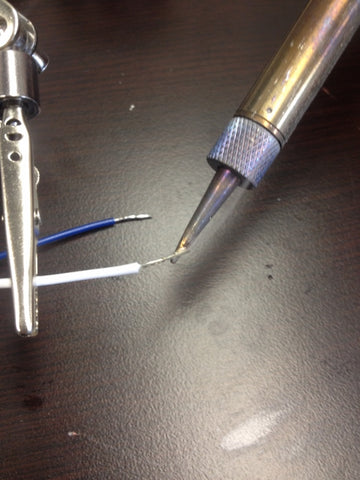
7. Next, you will need some heat-shrink tubes. We used 1/8" to cover our diodes. Use a lighter or hairdryer to start heating it up. Remember to move the heat evenly to prevent damage and overheating, which could melt the parts while heating. You'll know you're done once the tube is form-fitting and covers everything important.

8. Time for some crimping. The switches and other connections require the crimping of some push-on connectors. Our solder ends from earlier will fit perfectly into the connector. If you do not have a crimping tool then use some pliers with a flat area to flatten the connector. Make sure it's nice and tight. (You can find these connectors, along with wires and diodes in our handy wiring kit).

9. Almost there. We need to wire up the system now to make sure everything works fine. We used a multimeter/voltmeter to check and see that the relays were giving +12 VDC and -12 VDC with each system. The electrical drawing for wiring is available here. (We used a terminal strip to make the circuit cleaner and simpler but it is not necessary for a system to function).

10. Once you confirm that everything is working correctly you'll be ready for installation! Below is a photo showing off all the circuitry a little more clearly for you.

All done! Hopefully, you found this helpful but if you happen to have any other inquiries remember we are always available to answer any questions or concerns you may have.